PEEK continuous extrusion capillary
> PEEK is widely used in analytical instruments and semiconductor industry due to its excellent chemical stability and corrosion resistance.
Industry, such as chromatographs, analyzers, sequencers and other testing equipment pipelines.
> High toughness, high strength PEEK capillary tube is formed by continuous extrusion process, with good dimensional stability and can be connected
Continue to extrude and mold for thousands of meters without breaking.
PEEK medical catheters have good insulation properties, and a single side of 0.2mm can reach an insulation strength of 5KV. At the same time, PEEK has an extremely low moisture absorption rate, and its insulation strength will not be affected in a humid environment or high-temperature cooking.
It can adapt to all the sterilization methods commonly used in medicine. Because of its columnar stiffness and thin wall, the bending radius is very small, which helps to manipulate the tortuous path of the catheter through the body. The material can be sterilized using gamma, ethylene oxide (EO or EtO), electron beam or autoclave.
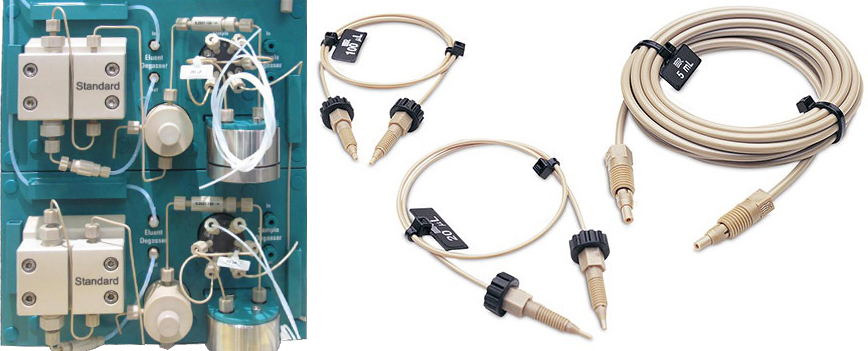
These include: cardiac puncture surgery, varicose vein radiofrequency ablation, cardiac radiofrequency ablation, minimally invasive abdominal devices, etc.
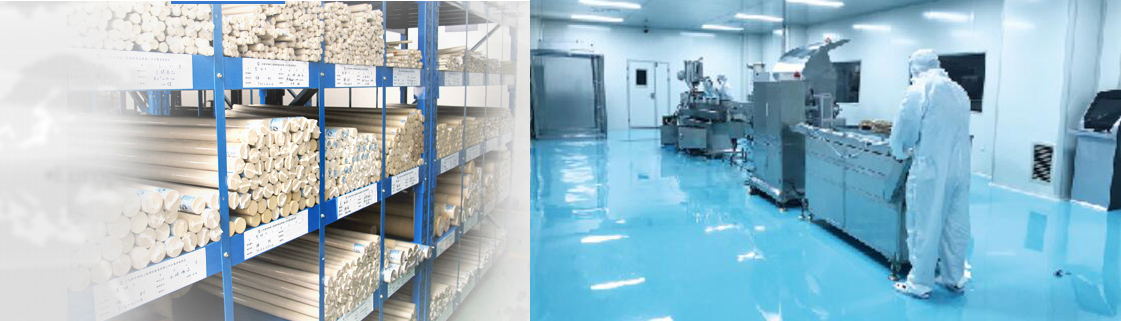
2. Catheter printing: scale printing, ring printing
3. Catheter drilling: round hole, elliptical hole, through hole, single-sided hole, square hole, special-shaped hole (aperture range 0.1-10mm)
4. Catheter shaping: Catheter bending, catheter shaping at different angles and shapes.
PEEK Introduction and Characteristics
Polyetheretherketone resin (PEEK resin for short) is a new type of semi-crystalline aromatic thermoplastic engineering plastic made by condensation reaction of 4,4′-difluorobenzophenone and hydroquinone in the presence of alkali metal carbonate and diphenyl sulfone as solvent. It is a high temperature resistant thermoplastic plastic with a high glass transition temperature (143℃) and melting point (334℃), and a load heat deformation temperature of up to 316℃ (30% glass fiber or carbon fiber reinforced grade). It can be used for a long time at 250℃. Compared with other high temperature resistant plastics such as PI, PPS, PTFE, PPO, etc., the upper limit of the use temperature is nearly 50℃ higher;
our company supplies imported PEEK rods, carbon fiber PEEK rods, PEEK plates, PEEK sheets, PEEK films, PEEK pipes, PEEK rings, PEEK capillaries, PEEK plate processing, PEEK plate customization, PEEK high temperature wear-resistant rods, carbon fiber PEEK rods, and glass fiber PEEK rods. Quality guaranteed, welcome to negotiate. Rod φ1~φ200mm, capillary 1/16, 1/8, plate 1030*600* (5~200), thin sheet 0.2, 2, 5mm
1. High temperature resistance PEEK has a high glass transition temperature and melting point (334°C), which is one of the reasons why it can be reliably used in applications requiring heat resistance. Its load heat deformation temperature is as high as 316°C, and the continuous use temperature is 260°C.
2. Wear resistance PEEK materials have good wear resistance in harsh environments such as high temperature, high load, and strong corrosion.
3. High strength PEEK has good mechanical strength, toughness and rigidity and is a balanced plastic. In particular, its excellent fatigue resistance to alternating stress is outstanding among all plastics and comparable to alloy materials.
4. Self-lubricating property PEEK has outstanding sliding properties among all plastics and is suitable for use in applications that strictly require low friction coefficient and wear resistance. In particular, PEEK modified by mixing carbon fiber and graphite in a certain proportion has better self-lubricating properties.
5. Chemical resistance (corrosion resistance) PEEK has excellent chemical resistance. Among common chemicals, only concentrated sulfuric acid can dissolve or destroy it. Its corrosion resistance is similar to that of nickel steel.
6. Flame retardancy : PEEK is a very stable polymer. A 1.45 mm thick sample can reach a high flame retardant standard without adding any flame retardant.
7. Peel resistance : PEEK has good peel resistance, so it can be made into thinly coated wires or electromagnetic wires and can be used under harsh conditions.
8. Fatigue resistance : PEEK has the best fatigue resistance among all resins.
9. Electrical properties PEEK can maintain stable and excellent electrical properties over a wide range of temperature and frequency.
10. Radiation resistance : It has a strong ability to resist gamma radiation, which exceeds that of polystyrene, which has good radiation resistance among general resins. It can be made into high-performance wires that can still maintain good insulation ability when the gamma radiation dose reaches 1100 Mrad.
11. Hydrolysis resistance PEEK and its composite materials are not chemically affected by water and high-pressure steam. Products made of this material can still maintain excellent properties after continuous use in high-temperature and high-pressure water.
Contact Us Now and Enjoy a One-Stop Solution!
Fill the Form to Get a Quote, Product Manual, Performance Parameters, Custom Solutions, Technical Consultation, and Samples